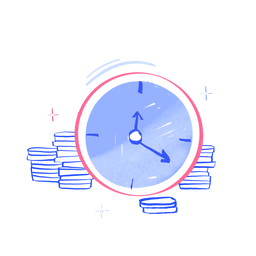
We could not find any results for:
Make sure your spelling is correct or try broadening your search.
Share Name | Share Symbol | Market | Type | Share ISIN | Share Description |
---|---|---|---|---|---|
Plantic Tech. | LSE:PLNT | London | Ordinary Share | AU0000XINEG8 | ORD NPV (DI) |
Price Change | % Change | Share Price | Bid Price | Offer Price | High Price | Low Price | Open Price | Shares Traded | Last Trade | |
---|---|---|---|---|---|---|---|---|---|---|
0.00 | 0.00% | 7.75 | 0.00 | 01:00:00 |
Industry Sector | Turnover | Profit | EPS - Basic | PE Ratio | Market Cap |
---|---|---|---|---|---|
0 | 0 | N/A | 0 |
TIDMPLNT RNS Number : 5482I Plantic Technologies Limited 15 March 2010 Plantic Technologies Limited ("Plantic" or "the Company") Audited results for year ended 31 December 2009 Plantic (AIM:PLNT), the technology company engaged in the development and commercialisation of a range of environmentally friendly plastics from renewable resources, today announces its results for the year ended 31 December 2009. Key Points · Closing cash position at 31 December 2009 was A$15.6m. · Net cash outflow reduced from A$11.8m in 2008 to A$10.3m in 2009. · Cash used in operations reduced from A$10.9m in 2008 to A$8.6m in 2009 · Operating loss (excluding financing and currency fluctuations) reduced from A$11.7m in 2008 to A$11.1m in 2009. · Net loss of A$10.8m (2008 A$9.0m), in line with market expectations. · Cost reductions of A$1m achieved in 2009. · Revenue decreased to A$1.2M, primarily caused by lower sales to our former partner DuPont and as a result of the difficult trading conditions experienced in Europe in 2009 · Post balance date KlöcknerPentaplast appointed as Plantic's distributor of rigid film replacing DuPont and launch of a new high renewable content product range branded eco Plastic(TM) Brendan Morris, Chief Executive Plantic Technologies, comments: "2009 was a difficult year for Plantic and many other companies in the plastics industry. Economic conditions in our major markets impacted both on the competitiveness of our products and on the ability of our partners and potential customers to allocate resources to developing new products. "To date in 2010, Plantic has seen activity increase and expects further commercial success by working with its new partner Klockner Pentaplast to obtain new customers. It will also be offering its high renewable content polymer product eco Plastic(TM) as an alternative to its existing customer base and moving into new markets. "Our revised business model, with its emphasis on higher margin royalty streams and a reduced cost base, is both lower risk and more competitive. In the longer term, the decisive action we have taken leaves Plantic well positioned to exploit commercial opportunities arising from a basic need for packaging and other materials with a lower carbon footprint." FURTHER INFORMATION: +-------------------------------+---------------------------------+ | Plantic Technologies: | | +-------------------------------+---------------------------------+ | Brendan Morris, Chief | +61(0)3 9353 7983 | | Executive Officer | | +-------------------------------+---------------------------------+ | | | +-------------------------------+---------------------------------+ | Nomura Code Securities | | | Limited: | | +-------------------------------+---------------------------------+ | Juliet Thompson / Giles | +44 (0)20 7776 1204 | | Balleny | | +-------------------------------+---------------------------------+ | | | +-------------------------------+---------------------------------+ | Pelham Bell Pottinger: | | +-------------------------------+---------------------------------+ | Archie Berens | +44 (0)207 337 1509 / +44 | | | (0)7802 442486 | +-------------------------------+---------------------------------+ | Sam Boston | | +-------------------------------+---------------------------------+ CHAIRMAN'S REPORT 2009 The Chief Executive Officer's report highlights the specific achievements and reviews of Plantic's financial and operational performance during 2009. Introduction Plantic's original success was founded on a major break-through technology, now covered by international patents. This technology enabled the Company to manufacture plastics with a wide variety of applications via modification of natural, high-amylose starches. The unique low-energy process based on a sustainable annual crop, with an outstanding "carbon footprint", together with the biodegradability (even in domestic compost) has won the attention of major retail brand-owners throughout the world. Having proved the commercial viability of our product, we sought to gain market share from packaging and other products made from conventional petrochemical-based polymers, well entrenched in supply chains. We enjoyed considerable success in persuading several of the world's leading brand owners that our product provides a genuine and practical alternative to conventional plastics. We also showed them how they can offer their own customers a means of reducing their carbon footprint through its use. Companies that used Plantic products included major brand owners and retailers such as Cadbury, Sainsbury's and Marks and Spencer. However, the significant reduction in oil prices since July 2008 made it difficult for Plantic to compete on price with conventional plastics. With our customers also coming under cost pressures, compounded by the effects of the global financial crisis, this inevitably led to a reduction in sales of our material. Nowhere was this more apparent than with our largest customer and most important distributor, DuPont Industries. The impact of the global financial crisis severely affected DuPont and reduced their ability to promote and re-sell Plantic products in the key North American markets, although we did gain a new customer of sheet material, namely Key Baby, which launched a range of BPA-free baby products packed in Plantic. Strategy In this economic environment, we realised that our most urgent priority was to reduce our cost base as quickly as possible, in order to be able to price our product more competitively. We took decisive action to achieve this and our executive team deserve credit for their efforts in reducing general and administrative expenses. We have also carefully managed our cash and retain a healthy balance sheet position as a result. In spite of this, we have continued to invest in ongoing research and product development, vital in maintaining our technological advantage. The second main element of our strategy has been to reduce transportation costs. It had always been our plan to have a manufacturing capability in Europe, to enable a more cost effective and efficient means of penetrating that important market. We therefore established a small, but highly efficient thermoforming plant in East Germany to provide Plantic sheet to major brand owners throughout Continental Europe and the UK. This became operational in February 2009 and is generating sales. Over the last 2 years, we have partnered with National Starch, who have consistently supported us. As previously stated, all markets are now under increasing pressure to switch to more sustainable raw materials with strong environmental credentials and a low carbon footprint. National Starch have always believed that Plantic material can become the leading bio-polymer in achieving this objective. Not only are they the exclusive supplier of our raw material, but they also work with us on the development of a broad range of new products. National Starch's ongoing support is evidenced by our most recent agreement with them, which we announced in December 2009. Plantic is working to relocate one of our existing base resin extrusion lines to the USA adjacent to the National Starch plant, which will enable us to be more cost competitive. This marks the next phase in Plantic's development with focus on low cost manufacturing close to the starch source, coupled with industry leaders as Plantic's distributors and future licensed manufacturers of final resin and sheet products. We will also be able to collaborate much more closely with National Starch, both on sales and marketing initiatives and on product development. The scope, capacity and implementation timeline of the relocated base resin plant is currently being finalised. We are pursuing the opportunity to gain US government funding as well as potential contributions from our partners and service providers to reduce the capital requirements. It is expected that Plantic will need to raise additional capital in order to allow the Company to complete its current strategy. Events since 31 December 2009 Since the close of the 2009 year, we have announced the next phase of our marketing plan, through a new partnership with Klockner Pentaplast, the leading manufacturer and marketer of rigid sheet throughout the world. This builds on the introductory marketing work carried out in conjunction with DuPont, who are co-operating in an orderly customer handover. Klockner will initially sell Plantic's sheet product in the Americas, but has the right to manufacture the material under licence in the future. Partnering with a more specialised packaging business will provide the requisite focus and drive to our sales efforts, especially as we have already taken the necessary steps to reduce costs. In February, we launched our new eco Plastic(TM) resin specifically designed to blend with conventional polymers to yield a lower energy and carbon footprint, and provide a significant renewable content. We are also working towards a partnership agreement for the compounding and global marketing of our injection and blow moulding resins with a global leader in manufacturing and marketing compounded resins throughout the world. Many major international brand owners are keen to incorporate significant percentages of biopolymers (renewable content) with conventional plastics, thereby providing environmental benefits, yet maintaining some key functional properties. This has provided exciting new opportunities for Plantic as we have been successful, beyond initial expectations, with Plantic products in co-extrusion, lamination or straight blending of our materials with conventional plastics. Outlook These key initiatives towards achieving our long term strategic business plan have the full endorsement of the board, and represent the desired direction for Plantic: to be the developer and licensor of our patented technology, gaining income from manufacturing royalties and marketing commissions at a higher margin than previously to the ultimate benefit of all shareholders. Plantic has taken the necessary steps to meet the ongoing competitive environment, and exploit the unique and desirable benefits from Plantic's biopolymers. The Directors therefore remain confident about the long-term prospects for the company and its technology. Ian Wightwick Chairman 15 March 2010 CHIEF EXECUTIVE'S REPORT 2009 was a difficult year for Plantic and many other companies in the plastics industry. Economic conditions in our major markets impacted both on the competitiveness of our products and on the ability of our partners and potential customers to allocate resources to developing new products. However, proactive cost reductions and improved working capital helped significantly reduce the cash burn compared to 2008. Conditions have improved and the appointment of Klöckner Pentaplast as our distributor of rigid sheet replacing DuPont and the launch of our new eco Plastic(TM) range is expected to see revenue and financial performance improve in 2010. OPERATING AND FINANCIAL REVIEW Commercial Progress Plantic products during 2009 were used commercially by major brand owners in Australia, and Europe and, for the first time in the USA, as Key Baby launched a range of BPA free baby products packed in Plantic. Trials by global brand owners progressed throughout the year. However, the conversion of projects into sales was slower than anticipated due to the global economic downturn. With over 40 major customer projects and trials currently in various stages of progress for rigid sheet, injection moulding and flexible film applications across Australia, Europe and the US, we expect further adoptions of Plantic materials in 2010 in a range of new applications, including confectionary, biscuits and industrial products. Plantic continued to strengthen its sales resources in Europe and the USA to support sales growth and brand owners marketing. This coupled with our investment in Thermoforming capability in Jena has resulted in increased interest for Plantic products. Plantic's Jena facility became operational in February 2009. In November 2009, Adept Limited, New Zealand's leading plastics product development and manufacturing company in the meat industry, introduced new biodegradable lamb plugs made possible through the advanced biopolymer technology of Plantic. Adept chose the Plantic resin for its unique functional and environmental benefits. The Adept / Plantic Lamb Plugs are fully biodegradable, water dispersible, home compostable and compostable to European (EN 13432) and American (ASTM 6400) standards. Since year end, Adept have successfully commercialized a new biodegradable beef throat plug based on Plantic resin and sales have already been made to abattoirs in NZ, Australia and the UK. In February 2010, Plantic announced the appointment of Klöckner Pentaplast, a leading global producer of rigid packaging films,as its distributor of Rigid Film, replacing DuPont. Klöckner will market and sell Plantic rigid packaging films throughout the Americas under its Pentafood Biofilm(TM) brand name. Designed to increase market penetration and enhance service to the marketplace, this partnership will provide customers with access to products that will help meet their sustainable packaging goals. Plantic will continue to service the Australasia and European markets directly. Product Development The Company's patented technology is based on the corn-starch derived amylose molecule, the chemical properties of which allow for a range of applications, including thermoforming, injection moulding, film extrusion and blow moulding, as well as rigid and flexible packaging, spraying, foaming and weaving. To complement this range of fully biodegradable plastics, Plantic has launched a new range of resins targeting the increasing global demand for sustainable plastic solutions that feature a high degree of renewably sourced material. Branded eco Plastic(TM), the new product line has been designed to meet the growing world demand for a sustainable approach to plastics technology, based on a high content of renewable material that will reduce carbon emissions and deliver exceptional performance characteristics across a broad range of applications. The key advantages of eco Plastic(TM) are that it contains approximately 40% renewable content, uses 25% less energy to manufacture than conventional polymers, significantly reduces carbon dioxide emissions, and is compatible with conventional processing aids and colorants in Blown Film, Injection Moulding and Extrusion Blow Moulding applications. eco Plastic(TM) has been designed as a sustainable solution to the needs of all traditional markets where environmental, functional and/or commercial requirements are not being met through conventional polymers. Blown Film, Injection Moulding and Extrusion Blow Moulding producers can all benefit from this technology. Intellectual Property Plantic's intellectual property portfolio continued to expand in 2009, with the granting of our fourth US patent supporting our core High Amylose Starch Technology. In addition, our recent patent applications covering High Amylose Injection Molding and Films technology have progressed to national phase examination in the USA, Europe and Japan. During 2009, we also filed a new patent application to protect a novel technology development supporting use of our High Amylose Starch-based materials in Injection Molding applications. Operational Performance The group's focus on health and safety record has always been of the highest priority, enabling Plantic to outperform its industry peers. The executive team remains vigilant to continue to demonstrate leadership in this crucial area. Significant investment continues to be made in new plant and equipment, with a view to improving the quality of Plantic products as well as the output and efficiency of the production process. Revenue was A$1.2m (2008 A$3.6m). Plantic's sales primarily decreased as a result of intial product development volumes sold to DuPont in the prior year not being repeated. As announced, Plantic has addressed the marketing issue by appointing Klockner Pentaplast, a key industry leader, as distribution partner for rigid sheet replacing DuPont, and is well advanced to complete a similar agreement with another global partner to market Injection Moulding, Blow Moulding and other resins. Plantic has taken action to improve its competitiveness against highly volatile prices of conventional plastics by announcing plans to move the manufacture of Plantic's resin products to the US adjacent to National Starch, the supplier of our key starch raw material. Cash used in operations was A$8.6m (2008 A$10.9m) A$2.3m lower than 2008 and was due to reduction in working capital, cost reductions and the receipt of government grants. Cash and cash equivalents as at 31st December 2009 was A$15.6m (2008 A$26.4m). Cost management continued to be a key focus during this difficult economic climate and Plantic achieved a reduction of A$1m in overheads, with overheads excluding financing and currency exchange movements being A$7.7m in 2009 (A$8.7m 2008) The net loss increased to A$10.8m (A$9.0 2008). However, this was due to lower finance income and adverse currency movements compared to 2008, with cost reduction measures offsetting lower sales and the resulting under recover of fixed manufacturing costs. Operating losses, excluding financing and currency movements were A$11.1m in 2009 (A$11.7m 2008), A$0.6m lower than 2008. Significant changes in the state of affairs In 2009 Plantic completed its investment in the Jena facility (Eastern Germany) with the addition of thermoforming capability. This has improved Plantic's competitiveness and responsiveness to customers and brand owners. With the exception of this investment there were no other significant changes in the group's state of affairs during the year. Outlook Our recently announced strategy to relocate one of our existing base resin extrusion lines to the USA adjacent to our key starch raw material supplier, National Starch, will enable us to be more cost competitive. This marks the next phase in Plantic's development with focus on low cost manufacturing close to the starch source, coupled with industry leaders as Plantic's distributors and future licenced manufacture of final resin and sheet products. The scope, capacity and implementation timeline of the relocated base resin plant is currently being finalised. The likely one-off costs of the relocation are estimated to be between approximately A$3-5 million. Management is seeking to reduce the capital requirements of the company by pursuing the opportunity to gain US Government funding for the relocation as well as potential contributions from our partners and service providers. The initial financial modeling indicates the annualised ongoing savings to be gained by the relocation will far outweigh the initial set-up costs of the relocation. In 2010, Plantic will be striving for further commercial success by working with its new partner Klockner Pentaplast to obtain new customers. It will also be offering an alternative product eco Plastic(TM) to its existing customer base and moving into new markets. Our business model, with its emphasis on higher margin royalty streams and a reduced cost base, is both lower risk and more competitive. In the longer term, the decisive action we have taken leaves Plantic well positioned to exploit commercial opportunities arising from a basic need for packaging and other materials with a lower carbon footprint. Brendan Morris Chief Executive 15 March 2010 Statement of comprehensive income for the year ended 31 December 2009 +----------+----------+------------------------------------+---+--------------+-------------+ | | | | | | | | | | | CONSOLIDATED | +----------+----------+------------------------------------+---+----------------------------+ | | | | | 12 | 12 | | | | | | months | months | +----------+----------+------------------------------------+---+--------------+-------------+ | | | | | 31/12/2009 | 31/12/2008 | +----------+----------+------------------------------------+---+--------------+-------------+ | | | | | $ | $ | +----------+----------+------------------------------------+---+--------------+-------------+ | Sales revenue | | 1,010,641 | 3,557,816 | +----------------------------------------------------------+---+--------------+-------------+ | Government grants | | 203,899 | 74,174 | +----------------------------------------------------------+---+--------------+-------------+ | Cost of sales | | (1,053,454) | (3,577,004) | +----------------------------------------------------------+---+--------------+-------------+ | Engineering and manufacturing scale up costs | | (3,580,230) | (3,089,907) | +----------------------------------------------------------+---+--------------+-------------+ | Gross Profit | | (3,419,144) | (3,034,921) | +----------------------------------------------------------+---+--------------+-------------+ | Finance revenue | | 810,598 | 2,021,318 | +----------------------------------------------------------+---+--------------+-------------+ | Other income | | 22,438 | 1,032,928 | +----------------------------------------------------------+---+--------------+-------------+ | Other expenses | | (197,577) | - | +----------------------------------------------------------+---+--------------+-------------+ | Administrative expenses | | (2,934,766) | (3,029,594) | +----------------------------------------------------------+---+--------------+-------------+ | Selling Expenses | | (2,217,794) | (2,034,513) | +----------------------------------------------------------+---+--------------+-------------+ | Research and development expenses | | (2,208,789) | (2,767,086) | +----------------------------------------------------------+---+--------------+-------------+ | Share based payment expense | | (377,025) | (882,473) | +----------------------------------------------------------+---+--------------+-------------+ | Finance costs | | (310,054) | (260,626) | +----------------------------------------------------------+---+--------------+-------------+ | Loss before income tax | | (10,832,111) | (8,954,967) | +----------------------------------------------------------+---+--------------+-------------+ | Income tax | | - | - | +----------------------------------------------------------+---+--------------+-------------+ | NET LOSS FOR THE PERIOD | | (10,832,111) | (8,954,967) | +----------------------------------------------------------+---+--------------+-------------+ | | | | | | | +----------+----------+------------------------------------+---+--------------+-------------+ | Other comprehensive (expenses)/income | | | | +----------------------------------------------------------+---+--------------+-------------+ | Foreign currency translation reserve movement | | (952,281) | 523,474 | +----------------------------------------------------------+---+--------------+-------------+ | Other comprehensive (expenses)/income for the period net of | (952,281) | 523,474 | | tax | | | +--------------------------------------------------------------+--------------+-------------+ | Total comprehensive loss for the period | | (11,784,392) | (8,431,493) | +----------------------------------------------------------+---+--------------+-------------+ | | | | | | | +----------+----------+------------------------------------+---+--------------+-------------+ | | | | | Cents | Cents | +----------+----------+------------------------------------+---+--------------+-------------+ | Loss per share for loss attributable to the ordinary equity | | | | holders of the company: | | | + +--------------+-------------+ | | | | +--------------------------------------------------------------+--------------+-------------+ | Basic loss per share | | (13.58) | (11.23) | +----------------------------------------------------------+---+--------------+-------------+ | Diluted loss per share | | (13.58) | (11.23) | +----------+----------+------------------------------------+---+--------------+-------------+ Statement of financial position as at 31 December 2009 +--------+--------+--------+---+--------------+--------------+ | | | | | CONSOLIDATED | +--------+--------+--------+---+-----------------------------+ | | | | | 12 | 12 | | | | | | months | months | +--------+--------+--------+---+--------------+--------------+ | | | | | 31/12/2009 | 31/12/2008 | +--------+--------+--------+---+--------------+--------------+ | | | | | $ | $ | +--------+--------+--------+---+--------------+--------------+ | Assets | | | | +--------------------------+---+--------------+--------------+ | Cash and cash | | 15,603,189 | 26,400,386 | | equivalents | | | | +--------------------------+---+--------------+--------------+ | Trade and other | | 159,943 | 2,108,158 | | receivables | | | | +--------------------------+---+--------------+--------------+ | Inventories | | 4,250,085 | 3,865,580 | +--------------------------+---+--------------+--------------+ | Other current assets | | 183,064 | 835,080 | +--------------------------+---+--------------+--------------+ | Total Current Assets | | 20,196,281 | 33,209,204 | +--------------------------+---+--------------+--------------+ | Investments | | - | - | +--------------------------+---+--------------+--------------+ | Plant and equipment | | 12,098,592 | 12,133,610 | +--------------------------+---+--------------+--------------+ | Total Non-current Assets | | 12,098,592 | 12,133,610 | | | | | | +--------------------------+---+--------------+--------------+ | Total Assets | | 32,294,873 | 45,342,814 | +--------------------------+---+--------------+--------------+ | | | | | | | +--------+--------+--------+---+--------------+--------------+ | Liabilities | | | | +--------------------------+---+--------------+--------------+ | Trade and other payables | | 1,186,578 | 2,168,237 | | | | | | +--------------------------+---+--------------+--------------+ | Interest bearing | | 1,074,005 | 2,604,318 | | liabilities | | | | +--------------------------+---+--------------+--------------+ | Provisions | | 202,812 | 143,951 | +--------------------------+---+--------------+--------------+ | Total Current | | 2,463,395 | 4,916,506 | | Liabilities | | | | +--------------------------+---+--------------+--------------+ | Interest bearing | | 3,022,677 | 2,234,797 | | liabilities | | | | +--------------------------+---+--------------+--------------+ | Provisions | | 63,085 | 38,428 | +--------------------------+---+--------------+--------------+ | Total Non-current | | 3,085,762 | 2,273,225 | | Liabilities | | | | +--------------------------+---+--------------+--------------+ | Total Liabilities | | 5,549,157 | 7,189,731 | +--------------------------+---+--------------+--------------+ | Net Assets | | 26,745,716 | 38,153,083 | +--------------------------+---+--------------+--------------+ | | | | | | | +--------+--------+--------+---+--------------+--------------+ | Equity | | | | +--------------------------+---+--------------+--------------+ | Issued capital | | 76,314,128 | 76,314,128 | +--------------------------+---+--------------+--------------+ | Reserves | | 1,653,773 | 2,299,157 | +--------------------------+---+--------------+--------------+ | Accumulated Losses | | (51,222,185) | (40,460,202) | +--------------------------+---+--------------+--------------+ | Total Equity | | 26,745,716 | 38,153,083 | +--------+--------+--------+---+--------------+--------------+ Statement of cash flows for the year ended 31 December 2009 +-----+----------------------+--------+------------+-------+-----------------+------------------+ | | | | | CONSOLIDATED | +----------------------------+--------+------------+-------+------------------------------------+ | | | | | 12 | 12 | | | | | | months | months | +----------------------------+--------+------------+-------+-----------------+------------------+ | | | | | 31/12/2009 | 31/12/2008 | +----------------------------+--------+------------+-------+-----------------+------------------+ | | | |Notes | $ | $ | +----------------------------+--------+------------+-------+-----------------+------------------+ | Cash flows used in operating activities | | | | +--------------------------------------------------+-------+-----------------+------------------+ | Receipts from customers and related parties | | 4,681,552 | 3,156,304 | +--------------------------------------------------+-------+-----------------+------------------+ | Grants received | | 203,899 | 74,174 | +--------------------------------------------------+-------+-----------------+------------------+ | Payments to suppliers and employees | | (13,487,973) | (14,107,628) | +--------------------------------------------------+-------+-----------------+------------------+ | Net cash flows used in operating activities | | (8,602,522) | (10,877,150) | +--------------------------------------------------+-------+-----------------+------------------+ | Cash flows used in | | | | | | | investing activities | | | | | | +----------------------------+--------+------------+-------+-----------------+------------------+ | Purchase of property, plant and equipment | | (1,433,515) | (526,153) | +--------------------------------------------------+-------+-----------------+------------------+ | Payment for plant under construction | | (1,032,084) | (4,310,203) | +--------------------------------------------------+-------+-----------------+------------------+ | Capital subsidies received | | 1,034,569 | | | | | | - | +--------------------------------------------------+-------+-----------------+------------------+ | | | | | | | +----------------------------+--------+------------+-------+-----------------+------------------+ | Net cash flows used in investing activities | | (1,431,030) | (4,836,356) | +--------------------------------------------------+-------+-----------------+------------------+ | Cash flows from financing activities | | | | +--------------------------------------------------+-------+-----------------+------------------+ | Interest paid | | (310,054) | (260,626) | +--------------------------------------------------+-------+-----------------+------------------+ | Interest received | | 800,044 | 3,124,694 | +--------------------------------------------------+-------+-----------------+------------------+ | Repayment of bank borrowings | | (957,433) | (715,250) | +--------------------------------------------------+-------+-----------------+------------------+ | Proceeds from bank borrowings | | 215,000 | 1,800,000 | +--------------------------------------------------+-------+-----------------+------------------+ | Net cash flows from financing activities | | (252,443) | 3,948,818 | +--------------------------------------------------+-------+-----------------+------------------+ | Net increase/(decrease) in cash and cash equivalents | (10,285,995) | (11,764,688) | +----------------------------------------------------------+-----------------+------------------+ | | | | | | | +----------------------------+--------+------------+-------+-----------------+------------------+ | Cash and cash equivalents | | | | +--------------------------------------------------+-------+-----------------+------------------+ | | - net foreign exchange differences | | (511,202) | 162,698 | +-----+--------------------------------------------+-------+-----------------+------------------+ | Cash and cash equivalents | | | | +--------------------------------------------------+-------+-----------------+------------------+ | | - at beginning of the year | | 26,400,386 | 38,002,376 | +-----+--------------------------------------------+-------+-----------------+------------------+ | | - at end of the year | | 15,603,189 | 26,400,386 | +-----+--------------------------------------------+-------+-----------------+------------------+ | | | | | | | | +-----+----------------------+--------+------------+-------+-----------------+------------------+ Statement of changes in equity for the year ended 31 December 2009 +----------------------+--------------+------------------+-------------------+------------------------+------------------+ | | Share | Issued | Foreign | Accumulated | Total | | | based | Capital | currency | losses | | | | payments | | translation | | | | | reserve | | reserve | | | +----------------------+--------------+------------------+-------------------+------------------------+------------------+ | CONSOLIDATED | $ | $ | $ | $ | $ | +----------------------+--------------+------------------+-------------------+------------------------+------------------+ | Balance at | | | | | | +----------------------+--------------+------------------+-------------------+------------------------+------------------+ | 1 January 2008 | 1,205,515 | 76,261,380 | (190,982) | (31,573,810) | 45,702,103 | +----------------------+--------------+------------------+-------------------+------------------------+------------------+ | Net loss for the | | | | (8,954,967) | (8,954,967) | | period | - | - | - | | | +----------------------+--------------+------------------+-------------------+------------------------+------------------+ | Other comprehensive | | | 523,474 | | 523,474 | | (expenses)/income | - | - | | - | | +----------------------+--------------+------------------+-------------------+------------------------+------------------+ | Total comprehensive | | | 523,474 | (8,954,967) | (8,431,493) | | loss for the period | - | - | | | | +----------------------+--------------+------------------+-------------------+------------------------+------------------+ | | | | | | | +----------------------+--------------+------------------+-------------------+------------------------+------------------+ | Transactions with | | | | | | | owners in their | | | | | | | capacity as owners | | | | | | +----------------------+--------------+------------------+-------------------+------------------------+------------------+ | Share Based Payment | 882,473 | | | | 882,473 | | | | - | - | - | | +----------------------+--------------+------------------+-------------------+------------------------+------------------+ | Vested options not | (68,575) | | | 68,575 | | | being exercised | | | - | | - | +----------------------+--------------+------------------+-------------------+------------------------+------------------+ | Increase in issued | (52,748) | 52,748 | | | | | capital | | | - | - | - | +----------------------+--------------+------------------+-------------------+------------------------+------------------+ | Balance at | | | | | | +----------------------+--------------+------------------+-------------------+------------------------+------------------+ | 31 December 2008 | 1,966,665 | 76,314,128 | 332,492 | (40,460,202) | 38,153,083 | +----------------------+--------------+------------------+-------------------+------------------------+------------------+ | | | | | | | +----------------------+--------------+------------------+-------------------+------------------------+------------------+ | Balance at | | | | | | +----------------------+--------------+------------------+-------------------+------------------------+------------------+ | 1 January 2009 | 1,966,665 | 76,314,128 | 332,492 | (40,460,202) | 38,153,083 | +----------------------+--------------+------------------+-------------------+------------------------+------------------+ | Net loss for the | | | | (10,832,111) | (10,832,111) | | period | - | - | - | | | +----------------------+--------------+------------------+-------------------+------------------------+------------------+ | Other comprehensive | | | (952,281) | - | (952,281) | | (expenses)/income | - | - | | | | +----------------------+--------------+------------------+-------------------+------------------------+------------------+ | Total comprehensive | | | (952,281) | (10,832,111) | (11,784,392) | | loss for the period | - | - | | | | +----------------------+--------------+------------------+-------------------+------------------------+------------------+ | | | | | | | +----------------------+--------------+------------------+-------------------+------------------------+------------------+ | Transactions with | | | | | | | owners in their | | | | | | | capacity as owners | | | | | | +----------------------+--------------+------------------+-------------------+------------------------+------------------+ | Share Based Payment | 377,025 | | | | 377,025 | | | | - | - | - | | +----------------------+--------------+------------------+-------------------+------------------------+------------------+ | Vested options not | (70,128) | | | 70,128 | | | being exercised | | - | - | | - | +----------------------+--------------+------------------+-------------------+------------------------+------------------+ | Increase in issued | | | | | | | capital | - | - | - | - | - | +----------------------+--------------+------------------+-------------------+------------------------+------------------+ | | | | | | | +----------------------+--------------+------------------+-------------------+------------------------+------------------+ | Balance at | | | | | | +----------------------+--------------+------------------+-------------------+------------------------+------------------+ | 31 December 2009 | 2,273,562 | 76,314,128 | (619,789) | (51,222,185) | 26,745,716 | +----------------------+--------------+------------------+-------------------+------------------------+------------------+ The Directors do not recommend the payment of a dividend. The full annual Report will be posted to shareholders on 18th March 2010 and will also be available on the Company's website www.plantic.com.au. Copies will be available from that date from the Company's head office, 51 Burns Road, Altona, Vic, 3018, Australia and from the offices of Pelham Bell Pottinger. This information is provided by RNS The company news service from the London Stock Exchange END FR MMGMFLDNGGZM
1 Year Plantic Technologies Chart |
1 Month Plantic Technologies Chart |
It looks like you are not logged in. Click the button below to log in and keep track of your recent history.
Support: +44 (0) 203 8794 460 | support@advfn.com
By accessing the services available at ADVFN you are agreeing to be bound by ADVFN's Terms & Conditions