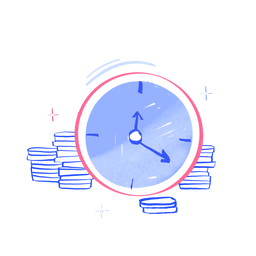
We could not find any results for:
Make sure your spelling is correct or try broadening your search.
Share Name | Share Symbol | Market | Type | Share ISIN | Share Description |
---|---|---|---|---|---|
Plantic Tech. | LSE:PLNT | London | Ordinary Share | AU0000XINEG8 | ORD NPV (DI) |
Price Change | % Change | Share Price | Bid Price | Offer Price | High Price | Low Price | Open Price | Shares Traded | Last Trade | |
---|---|---|---|---|---|---|---|---|---|---|
0.00 | 0.00% | 7.75 | - | 0.00 | 01:00:00 |
Industry Sector | Turnover | Profit | EPS - Basic | PE Ratio | Market Cap |
---|---|---|---|---|---|
0 | 0 | N/A | 0 |
Date | Subject | Author | Discuss |
---|---|---|---|
08/7/2010 11:43 | What's up here a few buyers, surely not ? LOL! Onwards & upwards from here, early bird takes all the gains! | ![]() ny boy | |
08/7/2010 08:46 | mm2 while the negatives are obvious, there's good news on the horizon: - US subsidy - K-P deal expansion - Resin trial update and deal with global leader - contract news - Further alliance with National Starch - loan from partner Importantly, unlike most other large players, National Starch's acquiror has no bioproduct subsidiary, so a tie-up with PLNT is still very much on the cards. BM knows the issues and I suspect the plan will be to push the share price upwards in this half of the year. The market cap is low and the story strong, so it wouldnt take much retail interest to lift the share price sharply.... | ![]() the_doctor | |
08/7/2010 08:24 | Couple of early buys today, 1 on lse for 18k and 1 on plus for 45k. Hopefully the turning point with the market? | ![]() themoneymonster2 | |
07/7/2010 10:30 | will have to be pretty extraordinary news to get this shareprice moving as we have the sword of damocles of a equity fundraise hanging over us. if alternative finance or a strategic investor were to fill the impending funding gap then maybe a different story..but in the meantime there are persistant sellers in the market and can unfortunately only see one way for the shares until funding resolved. any good news short term will be the point of a fundraise so dilution will occur at an effective pre news price. agree the company seems to be positioning themselves reasonably well though not judging that by actual revenue and have undoubtedly been relatively slow to market opportunity in a competitive environment...perhap | ![]() kooba | |
07/7/2010 09:10 | kooba Brendan is ok. He'll still get paid and doesnt really have any shares. Is is doing a very good job in terms of strategic positioning though. Bear in mind that Gordon Merchant is closely tied to the board I've also emailed Brendan. The expectation is that good news over the next few months will help lift the share price Funds may also come via a loan | ![]() the_doctor | |
07/7/2010 08:56 | Just a matter of time before investors twig that this is grossly under-valued! Patience require, when it moves up, it will be very fast moving. | ![]() ny boy | |
06/7/2010 09:27 | had contact with the company yesterday just pointed out the last rns Sales of product sold in the 5 months to the end of May have increased by approximately 80% compared to the second half of 2009, with revenues 50% higher. | ![]() divinausa1 | |
06/7/2010 09:18 | Kooba Cotact this guy at Matrix and tell him PLNT are not responding to your emails. He is the broker at Matrix dealing with PLNT, maybe he can answer your questions? stephen.mischler@mat | ![]() themoneymonster2 | |
06/7/2010 09:16 | btw mm2 still no response to my email sent on 29th june...not sure a new age of better communication is upon us yet! | ![]() kooba | |
06/7/2010 07:54 | Yep good luck tryin g to buy when it turns. I remember wanting 30,000 shares when the share price was 8.75p to buy and the mm's did not want to sell me any. Since then they have dropped the price on low volume and you can now buy quite a few at a time, probs up to 125,000 but when the share price turns they will turn the limits the other way. That's aim for you. Couple of big hitters on the shareholder list will wanting to be multi bagging, not selling at 5p. | ![]() themoneymonster2 | |
06/7/2010 06:42 | couple of players on the shareholder list! founder of ip group technology transfer pioneer. David Norwood Full name David Robert Norwood Country England Born 3 October 1968 Farnworth, near Bolton, Lancashire, England Title Grandmaster FIDE rating 2503 David Robert Norwood (born 1968) is an English chess Grandmaster,[1] chess writer, and businessman. The son of an electrician, Norwood read history at Keble College, Oxford University before joining city investment bank Banker's Trust in 1991. FIDE awarded him the International Master title in 1985 and the International Grandmaster title in 1989. He is less active as an over-the-board player these days, but maintains a strong interest in chess as a member of the Internet Chess Club. He has on a number of occasions captained, managed, or sponsored the England squad in major team events such as the Olympiad. Norwood has written several books including Winning with the Modern (the Modern Defence being a favorite opening of his) and Steve Davis plays Chess (co-authored with Steve Davis). He has also written many articles on chess for the Daily Telegraph. Norwood is Director of Special Projects at IP Group plc. He also made a large donation in 2001 to the British Chess Federation to assist with the development of junior chess. alan miller former star fund manager | ![]() kooba | |
06/7/2010 01:11 | PUGUGLY - 5 Jul'10 - 18:15 - 502 of 521 A real cash burner "Our cash position is expected to be approximately A$9.2m as at 30 June 2010" which at current exchange rates is £5,119,800 Thse boys look as though they are going to need refinacing as appear to have burnt through £6 million since this thread was started. Thanks to greengiant - 27 Jun'10 - 09:54 - 423 of 501. for some basic calculations - Cannot see any more reason to buy at this price than to buy PDX !!! ============== got into pdx at 38p now over 2 pounds in here after the trading update, which i think the market has overlooked(from the horses mouth Brendan Morris thinks so too!) time will tell.... | ![]() divinausa1 | |
05/7/2010 22:31 | Fair comment. All the best gg. | ![]() themoneymonster2 | |
05/7/2010 21:43 | tmm2. LOL - Yes I own FAN (over 4% actually), also own over 250k FDP shares, 15% of TND, 5% of RNSM and have just bought over £300k of RRL. I have some stinkers as well as some winners - luckily, life has been good and I have had more winners than losers. I made a lot of money in this sector, and I understand it. I posted on TIME stating that the product was not commercially viable. I posted on BPI stating that plastic costs had gone up, the next day the company released a IMS stating exactly that. The information I post is for information only, I hold no position. gg | ![]() greengiant | |
05/7/2010 21:23 | So around 30-40% of shares are in free float, rest are taken by institutions and private investors. Ony 80 million shares in issue currently. Probably will issue around 60-70 million shares around 7-8p to get the desired A$10 million. Still would only be 150 million shares in issue. | ![]() themoneymonster2 | |
05/7/2010 21:19 | SHAREHOLDERS Figure 11 summarises the main shareholders. Figure 11: Main Shareholders as at 31 March 2010 Shareholder Holding (%) Gordon Merchant 18.4 Lynchwood Nominees 9.1 UBS (Luxembourg) SA 5.6 Halifax Life 3.8 HSBC James Capel as principal 2.4 Swisscanto Equity Climate Invest 2.2 Alan Miller 1.5 Penson/Nomura Code private clients 2.0 Jolimont Capital 2.0 David Norwood 1.0 RAB Capital 2.0 Hermes Pension Management 1.7 KBC Funds 1.4 Ashcourt Private Clients 1.4 Barclays Bank (Suisse) SA Geneva 1.4 Lansdowne Funds 1.2 ANIMA Emerging Markets 1.2 EVO Nominees 1.1 KBC Funds 1.1 Citadel Investments BVI 1.1 Rowan Dartington Private Clients 1.1 Source: Plantic FINANCIALS AND VALUATION The 2009 financials reflect the difficulties experienced by the whole plastics industry plus the specific issues with DuPont. 2009 revenue was A$1.0m (2008: $3.6m) with a net loss of A$10.8m (2008: A$9.8m). Cash at the end of 2009 was A$15.6m. Our estimates for 2010 and beyond assume that the agreement with Klöckner Pentaplast produces results and show revenues increasing to A$5.7m in 2010 and A$17m in 2011. We estimate the company becoming profitable in 2013. We have modelled the company raising A$10m in 2010 at a price of 8p per share which leads to a dilution of 48%. Our valuation is based on a DCF analysis with a terminal value based on year six FCF and a WACC of 20% to reflect execution risk. In arriving at a target price of 19p we have assumed full dilution with the A$10m raising described above. Clearly achievement of rapid sales growth is essential to support our valuation and we announcements of sales progress will be catalysts for the share price. We also anticipate announcement of a partnership with a major compounder regarding ecoPlastic. Matrix Corporate Capital LLP One Vine Street London, W1J 0AH +44 (0) 20 3206 7000 | ![]() themoneymonster2 | |
05/7/2010 21:17 | In the UK all major retailers have made commitments to greater sustainability and in particular in the area of reducing the environmental impact of packaging. As well as the sustainability drivers, Sainsbury's note the volatility of oil prices and see bioplastics as a hedge against that volatility. Structure of the Industry In order to understand Plantics's business model it is important to understand the structure of the plastic packaging industry. Commodity resin producers supply resin to compounders who add colours, stabiliser and polymer packages to produce a polymer that meets the specific requirements of converters. Converters turn specific resins into a wide range of products through injection or blow moulding, rigid sheet production or film production. This structure is shown in Figure 10. RISK FACTORS We have identified the following risks to Plantic. Dependence on large partners: Although a strength, dependence on large partners can also be a weakness due to their slow decision making cycle and the fact that Plantic's business is only a tiny fraction of their total activities. Although the new agreements have very large potential they still have to be executed and deliver sales growth. Interest in sustainability issues declines: Although we consider this unlikely it is possible. Switch in favour of recycling as opposed to biodegradability: As we have seen there is conflict between biodegradability and recycling with some commentators and market players preferring to opt for total recyclability as opposed to biodegradability. We believe, however, that within the large and very diverse packaging market place there is room for both solutions. Oil price falls: The cost competiveness of Plantic's products is partly driven by the oil price and a low oil price will make it harder to compete with conventional oil derived plastics. Having reviewed the oil supply situation in some depth we consider that the oil peaking argument is correct and that we are likely to face oil supply constraints, leading to higher oil prices, once the world comes out of recession. Failure to obtain cost comparability with oil based plastics: Despite the powerful drivers in favour of bioplastics they are unlikely to obtain mass acceptance until they can achieve cost comparability with oil derived alternatives. Technology problems: The core Plantic technology is well proven and the development issues are around utilising it to produce specific functional requirements for different end users. We consider technology risk small. Plantic has already demonstrated that their products can be produced on conventional plastic industry machinery. Supply chain: Plantic's product is dependent on the supply of high amylose corn which is produced by National Starch in the USA and by Penford in Australia. Industrial starches have been grown for decades and are used in many applications. Compared to biofuels the amount of land required to supply current and projected needs is low and supply is on long-term contracts Execution: Although we believe that management has now adopted the correct strategy and the company is heading in the right direction there still remains execution risk. The next twelve months, and the evolution of the new agreements, remain critical for the company. MANAGEMENT Brendan Morris Chief Executive Officer Mr. Morris was appointed CEO in January 2008 having joined Plantic in 2004 as Finance Director and Chief Operating Officer. During his time at Plantic, Mr. Morris has played an instrumental role in Plantic's commercial and development agreements with Amcor, DuPont, National Starch and Bemis. He was also intimately involved in three capital raisings, including a successful listing on the Alternative Investment Market (AIM) of the London Stock Exchange. Prior to joining Plantic, Mr. Morris spent seven years with Basell Polyolefins as CFO for their Flexible Film and Resin businesses in Australia and Thailand. Basell is the world's largest producer of polypropylene and advanced polyolefins products, a leading supplier of polyethylene and catalysts, and a global leader in the development and licensing of polypropylene and polyethylene processes. During the same period, Mr. Morris was also a Board Director of PolyPacifc (a resin compounding business) with operations in Australia and Malaysia. Prior to joining Basell Mr. Morris was CFO of APV's Global Contracting and Engineering business based in London and before that in strategy, commercial and financial management roles with APV Sales and Engineering business based in Australia and then in Denmark. Prior to his management career in commerce, Mr. Morris was a senior accountant with KPMG in Melbourne. He holds a Bachelor of Commerce degree from Deakin University and is a member of the Institute of Chartered Accountants in Australia. Norbert-Rainer Schmidt General Manager, Europe Mr. Schmidt joined Plantic in October 2007 as the General Manager of the European division. Based in Jena, Germany, he oversees the company's operations and developments while continuing to develop business opportunities in this market. Mr. Schmidt is also the Managing Director of Plantic's subsidiary in Germany, Plantic Technologies GmbH. Before joining Plantic, Mr. Schmidt was the Managing Director of Pharmatec GmbH in Germany, Switzerland, Russia and the UK. Pharmatec provides the production, storage and distribution of pharmaceutical utilities. During his time at Pharmatec, the company's annual sales increased by 12 million. Between 1997 and 2003, Mr. Schmidt was the Managing Director of Sales, Marketing and Technology for several companies including: Weiss Klimatechnik GmbH; Weiss GWE GmbH; OOO Weiss Technik; and Weiss Klimatechnik Spooz. During this period, he was also Chairman of BDK Luft und Reinraumtechnik GmbH.Prior to this, Mr. Schmidt was the Managing Director of APV Engineering in Crawley, England. In this role, he supervised engineering, contracting, unit systems and service for the food, pharmaceutical and cosmetics industries. The pharmaceutical business was established under Mr. Schmidt's direction. Mr. Schmidt's previous roles also include: Managing Director of Anton Steinecker Maschinenfabrik GmbH; Technical Leader and Senior Project Manager at Fresenius; and Project and Sales Engineering roles at SMS Verfahrenstechnik GmbH and Colt International GmbH. Mr. Schmidt graduated from his Engineering degree with honours. He completed his Master of Science in Process Engineering and Energy at the University of Applied Science Giessen. Ian Wightwick Chairman of the board of directors, member of the Audit, Finance and Risk Committee and the Human Resources and Remuneration Committee Ian Wightwick was appointed to the board as an independent non-executive director and elected chairman in October 2006. Mr. Wightwick has had a 50-year career spanning technical, marketing, production, consulting, general management and chief executive roles in the oil, chemical, food and paper and packaging industries. Aside from his role at Plantic, his current activities include investment management, consulting and mentoring (both at national and international level). | ![]() themoneymonster2 | |
05/7/2010 21:16 | over how best to dispose of them and have now switched to 100% recyclable plastics. Despite these issues the market for bioplastics and biodegradable plastics is growing. The National Non-Food Crops Centre, in York, which co-ordinates British research into renewable polymers, has forecast that biodegradable plastics could make up 10% of the world's $1,600bn polymer industry by 2020. THE MARKET As Sam Knight of the FT said: "Plastics are the forgotten infrastructure that allows modern urban life to exist". The Global Plastics Market The global production of all plastics has grown significantly over the last 60 years, increasing from 1.5m tonnes in 1950 to 260m tonnes in 2007, a CAGR of 9.5% (source: PlasticEurope Market Research Group). In 2008, in response to the global financial crisis, production fell to 245m tonnes, the first time production had fallen since 1974. The industry expects growth to begin again as the world moves out of recession. Plastic prices also fell 3040% in 2008/09 but as shown in Figure 8 have now started to recover, in the case of LLPE (linear low density polyethylene) to c.$1,000/tonne compared to a low of c.$600/tonne and a peak of more than $1,700 per tonne in mid-2008. According to the Plastics Federation, in the UK plastic consumption has grown from c.2m tonnes in 1973 to c.5m tonnes in 2008 and c.35% of this consumption is for packaging. A 2008 PIRA study estimated that rigid plastics made up 25% of total packaging materials and flexible plastics 14% and demonstrated 6.3% and 6.2% growth respectively. Rexam plc, a leading packaging company, estimates that the global packaging market will grow 24% per annum in the foreseeable future and that the use of plastic is growing faster than any other material. The Market for Bioplastics and Biodegradable Plastics Statistics on the actual and potential markets for bioplastics and biodegradable plastics can be confusing due to differing use of definitions and the fact that biodegradable plastics includes non-bio, i.e. oil derived plastics that have been altered to be biodegradable. We have drawn on several sources here. In 2001, COPA (Committee of Agricultural Organisation in the European Union) and COGECA (General Committee for the Agricultural Cooperation in the European Union) undertook a market review of bioplastics which estimated that half of the six million tonnes of disposable plastic packaging in the European Union could be substituted by bioplastics. The bioplastics sector has seen rapid growth and the European Bioplastics (the trade association of the bioplastics industry), estimates that annual global production of bioplastics will increase six-fold to 1.5 million tonnes by 2011, up from 262,000 tonnes in 2007. It should be noted that this will still only be c.0.6% of total plastics production. The Helmut Kaiser Consultancy estimated in 2008 that the bioplastics market was growing at 810% per annum, was worth over $1bn in 2007, and expected to reach over $10bn a year by 2020. They also reported that there were over 500 bioplastics processing companies in the world, a number that was expected to reach more than 5,000 by 2020. A study by BCC Research estimated that the global market for biodegradable polymers increased from 186,000 tonnes to 246,000 tonnes in 2007 (32% growth) and is expected to reach 547,000 tonnes by 2012 (a CAGR of 17.3%). The sectors within this market are defined as: compost bags (45% in 2007), loose filled packaging (30%), other packaging (15%) and miscellaneous (10%). According to Jim Lunt & Associates (a business consultancy specialising in plastics), there are four applications have significant growth opportunities for bioplastics in the immediate future: Compostable single use bags/films Fibres, degradable and non-degradable Plastic foam cushioning blocks Bioplastic moulded products, degradable and non-degradable In December 2008, Plastics News reported that the market for bio polymer grew from $1.93bn in 2002 to $2.85bn in 2007 and that it is expected to grow to $4.02bn by 2012. Of the projected demand in 2012 approximately 24% is expected to be starch based polymer. Frost & Sullivan report that biopolymer demand rose from 50,000 tonnes in 2003 to c.85,000 tonnes in 2007, of which c.35,000 tonnes were starch derived. They estimate total demand for biopolymers growing to 390,000 tonnes by 2013, of which 150,000 tonnes will be starch derived. To synthesise these various reports, it is clear that the market for bioplastics is growing rapidly. Market Drivers The sustainability issues described above have in recent years come to the fore in the public consciousness and driven corporates to adopt policies and programmes aimed at improving sustainability. Although there is still a degree of "green washing" the corporate response, particularly from retailers and consumer goods companies, has largely evolved from a passive one only driven by compliance with regulations to an active stance aimed at gaining competitive advantage. In many cases (e.g. Walmart) companies have found that looking for sustainability improvements can also be profitable economic measures. | ![]() themoneymonster2 | |
05/7/2010 21:15 | Polyhydroxyalkanoate (PHA) PHA is a polyester produced by bacteria processing glucose or starch derived from sugars or plant oils. Polyamide 11 (PA 11) PA 11 is a biopolymer derived from natural oil. Bio-derived Polyethylene The basic building block of polyethylene is ethylene which can be produced from ethanol produced from the fermentation of agricultural feedstocks such as sugar or corn i.e. bio-derived. Synthetic Biodegradable Synthetic biodegradable plastics are oil derived plastics that have additives in to make them partially bio-degradable. It is notable that in 2009 both the SPI, the plastics industry trade association in the USA, formally came out in support of European Bioplastics position that claims that "oxo-biodegradable" plastics were biodegradable were incorrect as the degradation process in the case of oxo-biodegradable plastics was essentially one of fragmentation, breaking down into small pieces that remain in the environment. The characteristics of Plantic, PLA, PHA and synthetic biodegradable plastics are summarised in Figure 6. The figure shows that Plantic's material has a number of advantages over PLA, PHA and synthetic biodegradables. Sustainability As with most issues around sustainability, the realities around plastic use and bioplastics in particular are more complex than the simple, "bioplastics are good, conventional plastics are bad" views that some environmentalists would push. For businesses and individuals considering how to make their operations and life more sustainable it is necessary to consider the complete picture around any proposed development. Bioplastics have clear sustainability advantages in two main areas. Firstly conventional plastics are derived from oil and there are increasing concerns about the long-term supply of oil. Analysts vary in their estimates of when peak oil, the point at which oil production rates peak, may occur but the consensus seems to be in the 20102020 timeframe, a view reinforced by Fatih Birol, Chief Economist of the International Energy Agency in August 2009. In addition to the oil peaking concerns there is momentum, particularly in the USA, towards reducing dependence on imported oil driven by energy security concerns. Although plastic feedstock only accounts for 4% of oil use (plus an additional 3-4% used during manufacture) wider use of bioplastics would contribute towards reduction of oil dependence. The second sustainability factor is dealing with the end-of-life problem. Plastics are long-lived substances and their disposal and dispersal into the environment is an increasing concern. In the UK for instance, it is estimated by Waste Online that three million tonnes of plastic waste are disposed of per year and that 56% of this is used packaging. Plastic packaging makes up 7% of the average household waste by weight and | ![]() themoneymonster2 | |
05/7/2010 21:14 | If an agreement is reached with the leading compounder it will, like the Klöckner Pentaplast agreement, lead to both product sales and royalties. Elements of Strategy The agreements are components of a strategy that needs to be viewed in the context of the structure of the plastics industry in which commodity resin producers sell resin to compounders who add colours, stabilisers and polymer packages to tailor the polymer characteristics to the requirements of the customer. Compounders then supply converters who turn the polymer into products which can be either injection or blow moulded, rigid sheets or films. The Klöckner Pentaplast agreement links Plantic to a global leader in the rigid sheet market segment. An agreement with a leading compounder would give access to a global market of converters. Plantic's strategy is moving it away from being a manufacturing company with high costs to becoming a royalty based licencing company with product development R&D. BIOPLASTICS History Bioplastics are not new. Parkesine, the first man-made polymer,was invented by Alexander Parkes in 1856 and was synthesised from chloroform and castor oil. In 1941 Henry Ford unveiled a "soy bean" car with soy based plastic body panels. In the last decade, however, we have seen increasing attention being focused on bioplastics as sustainability issues have come to the fore. Definitions A bioplastic is a synthetic polymer derived from a renewable biomass source such as pea starch, corn starch, potato starch, vegetable oil or even microbiota. This is in contrast to a traditional plastic which is derived entirely from petroleum. To be classified as a bioplastic the material must be organic and contain some percentage of recently fixed (new) carbon found in biological resources or crops. This definition is the basis of a US standard, ASTM D6866. There is sometimes confusion between bioplastics and biodegradable plastics. Biodegradable or compostable plastics are those which meet scientifically recognised norms for biodegradability and compostability of plastics and plastic products, independent of their carbon origin. Biodegradability means that the material can be degraded by microbes under the right conditions. Non biodegradable bioplastic are referred to as durable. The degree to which a product biodegrades varies according to how stable the polymer is, the temperature, and how much oxygen is available. In Europe the composting standard is EN 13432 and in the USA ASTM D6400. To meet the ASTM and EN standards the material must 60% biodegrade within 180 days in specified composting conditions and third party certification is required. Bioplastics and biodegradable plastics are not mutually exclusive. Some petrochemical based plastics are termed biodegradable as their composition has been altered to enable degradation. Traditional plastics such as polyethylene are degraded slowly by ultraviolet light and oxygen and the manufacturers usually add stabilising chemicals. Degradation agents are then added to the plastic in order to achieve a controlled disintegration process. This plastic is known as degradable plastic or oxy-degradable plastic or photodegradable plastic. These "oxo-plastics" go through a disintegration process followed by a biodegradation. Manufacturers of such plastics claim that their plastics will be broken down by microbes, however the products do not meet the EN13432 composting standard and therefore cannot be classified as biodegradable. They can, however, meet a safety and performance standard, ASTM D6954-04. Types of Bioplastics Starch Based Starch based bioplastics use starch as the basic polymer. Plantic's products are derived from high amylose maize. Polylactic Acid (PLA) PLA is a transparent plastic obtained from the fermentation of cane sugar or glucose. | ![]() themoneymonster2 | |
05/7/2010 21:14 | COMMERCIAL PROGRESS Manufacturing Plants Plantic's original manufacturing plant was in Melbourne, Australia. In November 2008 Plantic established its second manufacturing facility in Germany to serve the European and North American markets. The plant has a thermoforming operation which allows rapid prototyping, more efficient customer trials and increased production capacity. In addition to Plantic products the plant can produce conventional plastics. In December 2009 the company announced an agreement with National Starch which covers the relocation of the manufacturing of Plantic to the USA. The plant will be co-located with the National Starch plant which will reduce total production costs by an estimated 25%. Commercial Agreements A chronology of Plantic's commercial agreements is shown below. DuPont In September 2007 Plantic entered into an agreement with DuPont Packaging and Industrial Polymers in the US for the global distribution of injection moulding resins (excluding Australia and New Zealand). The nature of the agreement stated that Dupont would also market Plantic's starch based sheet materials for trays and rigid packaging applications in North America. Furthermore the relationship entailed a collaborative development of new products which included cosmetics, personal care, food packaging trays, caps and containers. Having announced the marketing agreement in North America, this was extended to Japan in April 2008 and South America in September 2008. Dupont market Plantic's products under the DuPont Renewably Sourced Materials initiative (part of DuPont's strategy to double revenues from non-depletable resources to $8bn by 2015). More specifically, Plantic is marketed under the Biomax family of products. In June 2009 the company reported that sales under the DuPont agreement had been slower than expected due to major business restructuring within DuPont but that engagement had improved in H2 2009. Major stocking orders were completed in early 2009 and the first customer sales of Plantic product were completed in the USA. In September 2009 Plantic announced that its material is being used by DuPont to package BPA free baby bottles for the Weil Baby product line. Crucially, the inserts for the bottles are fully compostable and dissolve in water, thereby increasing their environmental credentials with the consumer. On 15 February it was announced that Klöckner Pentaplast would replace DuPont as distributer of Plantic's rigid film products in the Americas. Bemis In November 2007, Plantic announced an alliance with Bemis (NYSE BMS), a large flexible packaging company with sales of c.$3.8bn. The partnership was designed to machines lead to the co-development of new flexible packaging materials and covered distribution in the Americas. Targeted applications include flexible packaging for personal care and dry goods. Major Film Producers Plantic is also working with major film producers to develop new products. In addition the company reports that: It has won a significant contract for supply from the German plant which will initially be for conventional PET plastic but with opportunities to convert to Plantic. Major trial orders have been received from a multi-national confectionary company and this is expected to lead to commercial orders early in 2010. It had completed a one year trial with an international biscuit manufacturer for a biscuit tray and had agreed a roll out plan for another 30 products The first orders from a South American confectionary company had been received by DuPont. It had completed successful trial runs for global meat processing applications and commissioned production tooling. It was progressing development of a film product with the brand owner. Recent Strategy Developments Klöckner Pentaplast The agreement with Klöckner Pentaplast announced on 15th February replaces the agreement with DuPont to distribute rigid packaging film in the Americas and the company reports that DuPont is working with it and Klöckner Pentaplast to "assure a smooth customer transition". The agreement also encompass the sales and distribution of Plantic's biodegradable injection moulding resins, again taking over from DuPont and a transition plan has been agreed with DuPont. The Plantic rigid film products will be sold in the Americas as Pentafood Biofilm and Thermosplastic Starch film. Klöckner Pentaplast is according to its website, "one of the world's leading producers of films for pharmaceutical, medical device, food electronics and general-purpose thermoforming, as well as printing and speciality applications". The company has sales of over $1.6bn and is based in Europe but has global presence, with capacity of over 650,000 tonnes across 11 countries. Klöckner Pentaplast will distribute rigid sheet using Plantic and will commence manufacturing trials of the product with the intention of manufacturing under licence. Plantic is working with Klöckner Pentaplast to prove that Plantic's rigid sheet can be produced on existing production lines. If, as is expected, this is proven then global roll-out of Plantic manufacturing should be straight forward as it would not involve significant capex for Klöckner Pentaplast. As well as resin sales a royalty stream will be payable on end product sales of sheet products. In the first stage Plantic will continue to serve the Australasian and European rigid sheet markets directly but will continue to negotiate global coverage with Klöckner Pentaplast. ecoPlastic On 11 February Plantic announced that it is introducing a new product range, ecoPlastic. It is a range of compounded resins with low carbon content and high renewable content based on Plantic's resin. Several customers in Australia and Europe are reported to be testing the product. In addition Plantic has commenced an evaluation programme with a leading compounder with a view to concluding an agreement for ecoPlastic manufacturing and worldwide distribution. Plantic wil form the platform on which they can build a suite of new renewable sourced materials with unique performance properties. Another important point is that specialised compounds based on ecoPlastic will be IP protected giving manufacturers an advantage in the market. | ![]() themoneymonster2 | |
05/7/2010 21:13 | Formed from non-GM corn starch, non toxic, renewable and sustainable Water dispersible Marks and Spencer In January 2007, Marks and Spencer launched an initiative termed "Plan A" (so called because there is no Plan B). This £200m sustainability plan was designed to have an impact on every aspect of the company's operations and in March 2010 the company reiterated its commitment to sustainability. The original plan included such aspects as becoming carbon neutral by 2012, extend sustainable sourcing, increase ethical trading, send no waste to landfill, and help customers and employees become healthier. Combined with a desire to reduce packaging by 25% by 2012, Plantic offered a good solution. Further advantages for the company include: Biodegradable Home compostable Certified safe for disposal in soil (by AIB-VINCOTTE) Contributors to the M&S/Plantic project include Stäger, Switzerland, who are responsible for thermoforming the trays. In June 2008, the Swiss Chocolate Assortment packaging was selected as one of the winners of the 20th DuPont Awards for Packaging Innovation. Competition Frost & Sullivan identify six key players in the bioplastics market. Figure 4 sets out the companies, their polymer source, existing markets, emerging markets, ownership and market cap. | ![]() themoneymonster2 | |
05/7/2010 21:12 | One of the issues with bioplastics has been the ease of processing compared to traditional oil derived materials. Plantic's strategy has always been to produce material that is compatible with standard conversion technologies. Currently Plantic can be readily converted on industry standard conversion equipment for thermoformed and injection moulded products. Plantic has also trialed its barrier resin in co-extruded blow moulding equipment and injection stretch blow moulding machines, as well as its flexible film formulations on cast and blown film conversion equipment. Forming of Plantic trays takes place on standard pressure forming machines and vacuum/pressure forming machines with modified heating systems to ensure that the heating step does not dry the sheet. In the basic conversion process, sheet is heated on a thermal plate, formed into a mould with air pressure, cut, ejected from the mould and then stripped from the web. The web is the material left over after the trays have been stripped and is reground and fed back into the extruder. Plantic has demonstrated sheet production process up to 950mm wide on conventional machinery and with lines running at 400kg/h, comparable to conventional plastic sheet extrusion lines of the same width. The capital cost of a Plantic extrusion line is in line with a PET sheet line of the same output. Economics The economics of manufacturing Plantic are driven by the cost of corn, the cost of wet milling and extracting starch, and the cost of processing. The base corn is not traded but sold on contract which gives greater price stability. National Starch own the seed and contract grows the corn. The cost of the corn is driven by a 15% yield difference compared to commodity corn and competition for land. The cost of starch is driven by chemical modification costs, processing costs (energy and labour). Plantic has a contract with National Starch that has a quarterly price adjustment basis and an annual price adjustment for labour and energy costs. New Technologies The company is working on new technologies including; extrusion blow moulded containers, dissolvable packaging and industrial films and has just launched ecoPlastic. The ecoPlastic resin will allow speciality resin manufacturers to formulate IP protected resins with high renewable content to meet specific customer functional requirements. Product Case Studies Cadbury Schweppes and the Plantic R1 Tray Perhaps the most well know of Plantic's clients is Cadbury Schweppes. The company has collaborated with Plantic since 2002 to incorporate biodegradable technology into its packaging. Plantic supplies thermoformed R1 trays for Dairy Milk Tray, Cadbury Eden chocolate boxes and shelf ready packaging for the Cadbury Fun Filled Freddo. For Cadbury's, Plantic's technology offers certain inherent advantages such as: Anti-Static Biodegradable Compostable to European standards (EN 13432) | ![]() themoneymonster2 |
It looks like you are not logged in. Click the button below to log in and keep track of your recent history.
Support: +44 (0) 203 8794 460 | support@advfn.com
By accessing the services available at ADVFN you are agreeing to be bound by ADVFN's Terms & Conditions