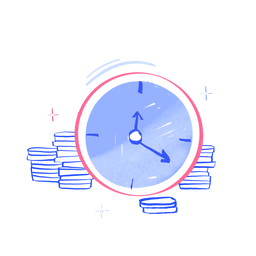
We could not find any results for:
Make sure your spelling is correct or try broadening your search.
Share Name | Share Symbol | Market | Type | Share ISIN | Share Description |
---|---|---|---|---|---|
Cropper (james) Plc | LSE:CRPR | London | Ordinary Share | GB0002346053 | ORD 25P |
Price Change | % Change | Share Price | Bid Price | Offer Price | High Price | Low Price | Open Price | Shares Traded | Last Trade | |
---|---|---|---|---|---|---|---|---|---|---|
0.00 | 0.00% | 265.00 | 260.00 | 270.00 | 265.00 | 265.00 | 265.00 | 6,159 | 08:00:00 |
Industry Sector | Turnover | Profit | EPS - Basic | PE Ratio | Market Cap |
---|---|---|---|---|---|
Paper Mills | 130.45M | 516k | 0.0540 | 49.07 | 25.32M |
Date | Subject | Author | Discuss |
---|---|---|---|
20/6/2006 08:20 | Disappointing that despite competitors disappearing Cropper were unable to grow turnover. However given extent of energy increase this was an decent performance. Prudent to cut dividend and dispose of perennial los maker - Pacofa. Greater transparency on Paper Mill Shop. Good returns from TFP. | ![]() capercaillie | |
18/6/2006 09:51 | Smith Anderson & Company Ltd (in Receivership) Restructuring 16 June 2006 Blair Nimmo and Tony Friar of KPMG Restructuring have been appointed as joint receivers of Smith Anderson & Company Ltd on 16 June 2006, at the request of the company's directors. Smith Anderson & Company Ltd, a wholly owned subsidiary of the Smith Anderson Group, one of Scotland's oldest manufacturing companies, had their papermaking operation at Fettykil Mills, Leslie in Fife. As a result of difficult trading conditions, the directors of the firm had implemented a restructuring plan last year that involved the closure of one papermaking machine and the loss of 70 jobs. Unfortunately, rising energy markets has seen UK gas and electricity prices continue to increase, and with forward prices being nearly 50% higher than when the rescue plan was formulated, the papermaking operation has become unsustainable. Joint Receiver and Head of Restructuring for KPMG in Scotland, Blair Nimmo, said: "The papermaking side of the group appears to have been in a challenging position for some time. A combination of high overheads and tough market conditions left the group's directors with no choice but to request the appointment of receivers." "It is regrettable, but the receivership has resulted in the closure of the two remaining paper machines on the Leslie site, and the current financial situation means that we have no option but to make 106 redundancies with immediate effect, with the exception of the Securecycle division, the papermaking buasiness has effectively now ceased to trade." Securecycle, a division which offers a waste collection and management service, is also affected by the receivership, however the joint receivers remain hopeful of achieving a sale of this part of the business. Nimmo continued: "Securecycle accounts for about £4m of the £27m turnover of Smith, Anderson & Co Ltd, and remains a growing and profitable part of the business. We would therefore encourage any potential buyer to make contact with us as early as possible." It should be emphasised that Smith Anderson Packaging Ltd is unaffected and will continue to trade as normal. | ![]() capercaillie | |
28/5/2006 10:54 | 42 jobs axed as mill shuts By Nigel McFarlane MORE than 40 people will lose their jobs with the closure of an operation at one of Bolton's oldest mills. Kruger Tissue Industrial's Bolton arm at the former Charles Turner paper mill is to close its doors next month because it is not making enough money. Manufacturing union Amicus, which represents 40 workers at the mill, was yesterday in negotiations with the company over the closure. continued... The mill, at Spring Side Mills in Belmont Road has operated since 1837. One mill worker, who asked not to be named, said: "One of Bolton's oldest manufacturers is going to close without a whimper. Kruger Tissue Industrial has deemed the site unprofitable. It's yet another manufacturer gone from Bolton forever." Around 40 jobs were shed in June 2004 as part of cost cutting measures, but some posts were relocated to Kruger sites in North Wales. The company, which manufactures 30,000 tons of tissue paper annually for UK workplaces, is one of three Kruger manufacturing sites in the UK. Other sites are in Penygroes, North Wales, and Church Stretton in Shropshire. Parent company Kruger, based in Montreal, is one of the world's largest manufacturers of paper and lumber products, including newsprint, tissue and wooden boards. The Belmont mill started production in 1837, and was taken over by Courtaulds in 1970. In 1983, Charles Turner & Co won a "caring employer" award but the company was hit by a strike the following winter. A management buyout of Charles Turner & Co took place in 1997 and the company merged with Kruger in May 2003, creating a company with a combined turnover of £40 million and 186 Bolton employees. Stuart Patterson, mill manager, said: "Regretfully Kruger Tissue Industrial Ltd announced on Friday, May 19 a proposal to cease manufacturing activities at their Springside Mills site in Bolton, due to incurring significant and sustained losses. The company, its employees and union representatives are now in a process of consultation in an attempt to find a solution." | ![]() capercaillie | |
25/5/2006 20:55 | Has anybody seen forecasts for this year? Im expecting grim reading but am taking particular interest in the turnover and whether they have been able to continue to grow the business. | ![]() capercaillie | |
15/5/2006 14:16 | Post removed by ADVFN | ![]() Abuse team | |
14/5/2006 09:48 | Papeteries de Cran has been ordered by the French courts to shut down within the next couple of months after going into liquidation on April 25. The firm is expected to shut up shop by June 25. The site and the equipment will then be sold off. In the meantime, Papeteries de Cran will continue to supply its customers as well as look for a potential last-minute buyer. The company was granted bankruptcy protection by the French courts on December 20. The firm was faced with difficulties meeting its financial obligations. Papeteries de Cran has already axed some 60 staff over the last 12 months. Just over 110 employees still work at the site. The company produces some 35,000 tonnes/yr of specialty paper and board grades on one 45,000 tonne/yr PM. | ![]() capercaillie | |
26/4/2006 13:33 | Post removed by ADVFN | ![]() Abuse team | |
16/4/2006 08:11 | well spotted cc | ![]() hybrasil | |
14/4/2006 19:26 | Cropper gain stockist Robert Horne Group is asserting its health awareness credentials by launching an anti-microbial manila board targeting the healthcare sector. Docugard is made using BioCote technology, which inhibits micro-organisms ike E. coli and MRSA, said the firm. Manilla is used for patient record cards, folders and charts, and Docugard comes in seven colours with 12 weight and size options. Visit: www.roberthorne.co.u | ![]() capercaillie | |
18/3/2006 08:00 | Gruppo Favini plans to close one of three paper machines at its Meerssen mill in the Netherlands. The group has not yet decided which unit to shut down, but expects to reach a decision within six weeks, following negotiations with trade unions. A spokesperson said, "The mill's capacity is too high and it needs to be adjusted to the requirements of the market." The group's CEO, Michele Paoli, said in a statement, "We take this step reluctantly, but it's one which has been forced upon us by structural changes within our marketplace and by the astonishing increase in energy and other input costs. By making Meerssen more cost-effective and productive, we create the platform for it to compete more successfully in the rapidly changing specialty marketplace." Around 140 people at the site will be affected by the move. The plant has a total specialty paper capacity of 25,000 tonnes/yr, churning out various grades including colored papers, uncoated graphic papers, text papers and cover papers. The mill houses three machines, PMs 2, 3 and 4, and each have a capacity of around 8,000 tonnes/yr. The group has one other plant in the Netherlands and two in Italy | ![]() capercaillie | |
07/3/2006 11:23 | Croppers pension scheme selling shares in... Cropper (as part of strategy to reduce equities). Doesn't look good though. Shares back to where they were before TW whipped them up on vacuous MBO chatter.... How effectively Cropper have dealt with energy costs will remain the short term driver IMO. Long term support around 140p by the looks of things. G. | ![]() garth | |
20/2/2006 21:32 | DS Smith proposes closure of its Sudbrook paper mill LONDON, Feb. 20, 2006 (Press Release) - As indicated at the Interim Results in December, a number of the Group's operations are under close scrutiny as a result of the difficult trading environment and high energy costs. DS Smith's UK Paper division, St Regis, has today announced the proposed closure of its Sudbrook Mill in Monmouthshire, which produces approximately 150,000 tonnes per annum of semi-chemical fluting paper, a speciality form of corrugated case material (CCM). It is proposed that the closure will be implemented by the end of May 2006. Sudbrook Mill is the most energy-intensive production operation within the Group and its annual energy costs have approximately doubled over the last three years. St Regis has been unable to pass this increase on to its customers and the mill is now making annualised operating losses of approximately £3 million. The decision to propose the closure of the mill has also been made in the context of demand for the mill's speciality product continuing to fall as customers switch to alternative lower-cost types of paper. Consultations have commenced with the mill's 135 employees and their representatives, with a view to reducing and mitigating the effects of the proposed closure. If the closure is confirmed following the consultation, every effort will be made to assist employees in finding alternative positions within the Group or with other employers in the area. It is estimated that the proposed closure will result in an exceptional charge to the profit and loss account in the financial year 2005/06 of the order of £22 million; approximately one third will arise from redundancy costs and other cash costs, and the remainder will be the write down of assets. It is anticipated that the cash outflow, which will occur in the financial year 2006/07, will be largely offset by asset sales and the realisation of working capital. The proposed closure of Sudbrook Mill is an important step towards raising the returns of the Group's UK Paper and Corrugated Packaging operations. Following the proposed closure of Sudbrook Mill, St Regis' principal mill at Kemsley will represent approximately 60% of the division's output of over 900,000 tonnes per annum; Kemsley Mill is ranked in the top quartile of European CCM mills in terms of cost competitiveness. | ![]() capercaillie | |
20/2/2006 21:30 | Sappi reviews future of Nash mill Andy Scott, 10/02/2006 The future of Sappi's Nash mill is under review, with the firm in consultation talks with staff and representatives, with 160 jobs in the balance. The South African fine paper producer has entered into a 90-day consultation period over the future of the Hemel Hempstead mill (pictured), which could lead to a relocation of production or its sale. Nash produces 30,000 tonnes per year of uncoated business papers, including the Croxley Heritage and Supreme, Vanguard, Paradis and Silken brands. Sappi Fine Paper Europe chief executive Wolfgang Pfarl previously announced an initiative entitled Everest to reduce costs and increase sales in Europe. Sappi said it was finding it increasingly difficult in the UK, due to escalating costs making the mill uncompetitive. Nash Mill's warehousing and sales facilities are not included in the talks. The mill has a history that dates back to the 1700s, and was purchased by Sappi in 1990. | ![]() capercaillie | |
20/2/2006 21:27 | Gas price surge fuels jobs cuts By Ruth Lythe The spiralling cost of gas has been blamed as a major factor behind a South Lakeland company being forced to cut 20 jobs. Bosses at James Cropper Plc said that a gas bill that was likely to reach £4 million for this financial year was one of the main reasons behind the move. However, it is hoped that those people whose posts are affected will be redeployed elsewhere among the 500-strong workforce at Burneside. For the full story, get the Gazette. John Denman, a director of the business, said that the paper mill was going through a "difficult situation" as it faced a gas bill expected to be double that of last year. The business uses gas to power its paper-making process and, without the energy source, Mr Denman said it would be unable to make paper. In addition, the company faced a big increase in its effluent treatment charges from United Utilities, which Mr Denman said was not caused by the cost of treating the firm's wastewater, but was to do with the need for the utilities giant to put in infrastructure throughout the North West. | ![]() capercaillie | |
19/1/2006 20:25 | A competitor to Docuguard? Garnett to launch MRSA-fighting paper in UK BRUSSELS, Jan. 19, 2006 (paperloop.com) - Garnett is set to introduce a paper to help combat methicillin resistant Staphylococcus aureus (MRSA), an antibiotic-resistant bacteria, blamed for 20% of deaths in UK hospitals from infections. The product's launch date is currently being finalized. The company said it could be 6-12 months before purchase tenders are made. The firm's Filemaster anti-bacterial range includes record cards, used by hospitals to note patient data. The paper will have an anti-bacterial inclusion, capable of killing MRSA. Cliff Barry, Garnett's executive vice chairman, said, "Filemaster will help reduce the transmission of the MRSA bug. As part of our research, we investigated demand for the material. It appears there is quite a lot of interest in it." He added, "For buyers, there is a cost to weigh up. The NHS [National Health Service] would pay a small premium for the material, which would reduce bacterial problems in hospitals. We imagine that they would want to buy it, because in the long run it is cheaper for them to use this product to prevent the spread of MRSA. But we can't be sure of what their reaction will be." MRSA can be transmitted from person to person fairly easily. In hospitals, there are usually many opportunities for MRSA to enter the body. Regular hand washing, the use of disposable gloves and coated dressings, and high hygiene levels can reduce cross infection. Garnett produces 15,000 tonnes/yr of specialty paper, including book and file coverings and envelope paper. The firm moved paper production from its Otley mill in North Yorkshire, UK, to unnamed plants in India and Africa at the end of last year due to a huge hike in its effluent treatment charges. | ![]() capercaillie | |
22/12/2005 18:29 | Credit Agricole now have a 6.42%. Is this the end of their buying? | ![]() capercaillie | |
06/12/2005 19:26 | capercaillie, thanks for those posts. Its interesting to read about some of the details relating to the measures being taken to reduce costs. Kind regards, G. | ![]() garth | |
06/12/2005 19:03 | Another paper casualty. Interesting increased holding announced today. Do they know something? Rigid Paper halts UK plant due to high energy prices BRUSSELS, Dec. 6, 2005 (paperloop.com) - Rigid Paper has suspended production at its 80,000 tonne/yr recycled containerboard mill in Selby, UK, due to escalating gas prices. The facility's two PMs were shut down on Friday. A company spokesman said the machines would remain idle until gas costs come down or until an alternative source of power is found. The firm is holding meetings today with a potential supplier of gas oil, which could enable the units to restart tomorrow. The spokesman explained that spot prices for gas have more than trebled of late, peaking at £1.70/therm ($2.94/therm), although they have now slipped back to £1.01/therm. "It is costing us £0.5 million extra per month to operate at present -- we are not talking small money here -- and we just can't continue like this," he said. "We have a reasonable amount of stock, but it can only last so long," the spokesman added. "These are difficult times for Rigid," he concluded, "but we are not alone in our suffering, another UK mill has had to shut down as well." The Selby plant's PM 1 has a capacity of 60,000 tonnes/yr of recycled containerboard, while PM 2 can make up to 20,000 tonnes/yr of recycled fluting | ![]() capercaillie | |
02/12/2005 07:53 | Curtis Fine Papers Paper navigates rough seas and holds a steady course for success Andy Scott, 01/12/2005 Despite tough times, Curtis Papers is implementing a plan of attack to get business back on track. With a history of paper making that dates back to 1873, independent Scottish speciality paper producer Curtis Fine Papers is now looking ahead to the future and the continued development of its workforce and product ranges. Managing director Keith Chapman (pictured), who took up his role six months ago, has already outlined his plan of action for the mill's ongoing development. Chapman replaced Alban Denton, who stepped down from his role as managing director with the St Andrew's-based firm in February this year. Like Denton, Chapman is a recruit from outside the firm, but he has gained an insight into how it operates from his role as managing director at reel-to-reel printer and paper bag manufacturer Bibby & Baron. Coming from outside of the business with a fresh perspective, Chapman says his new position has not been a million miles away from what he was doing before. "We have a team with a lot of experience in the paper industry, but there are advantages to not knowing everything," he says. Coming to grips with the ins and outs of the industry has been a steep learning curve, but it has not stopped him making tough decisions, one of the first being to implement a price increase. Although this may not have proved popular, Chapman believes it was overdue and necessary. The larger merchants were able to pass the increase on, and as Chapman explains, if nobody is making any money down the supply chain, it's not good for the industry. No major business was lost and although the company has forecast it will lose around £1.1m this year, the aim is to get back into profit. The signs are positive the company has made a profit in October for the first time in 16 months. "We are 100% owned by the directors with modest bank borrowing, and there's not many companies that can say that in the current climate," he adds. Quality control Chapman admits the closure and transfer of equipment and products from the firm's Dalmore mill in July last year has presented the firm with some quality issues, but adjustments are currently being made. "Our quality has not been as good as it could have been over the last six to nine months, and we are now looking to put that right." The approach has been for management to set targets, but as Chapman outlines, the company now intends to transfer more responsibility to the shop floor. A consultant has been brought in to help with this, and managers have been taken off site in order to become better coaches part of the firm's management programme. Chapman says that Curtis also intends to ensure that all of its ISO procedures are adhered to do, and one way the firm is doing this is by synthesising the number of tasks staff have to do, thus making sure they concentrate on the fundamental areas of the business. This has been helped by the award of over £60,000 from Scottish Enterprise Fife to jointly fund a series of business initiatives aimed at strengthening the firm's position as a major employer in the region. Dynamic changes The 18-month management programme, which encourages staff to focus on the changes ahead, will eventually include all managers and supervisors at the mill. "We operate in a dynamic and challenging market sector, and our success depends on embracing and implementing change." Some changes will be based simply on style, but he hopes even these will prove to be innovative. One plan is to launch at least 10 products every year. A decline in the graphical market led to the painful decision to close the firm's Dalmore mill last year, a decision taken before Chapman's tenure. Yet he admits that consolidation is not viewed as Curtis' route to salvation. "We need to make ourselves as competitive as we can be. There are enough niches in the market for Curtis to survive," he says. "Our job is to give people hope for the future and not to encourage complacency, as this is not a huge margin business," he adds. The firm needs to drive efficiency and, according to Chapman, its long-term position is secured by being in the right niche sectors. A further part of Curtis' development plans will be the appointment of a full-time buyer, who will be responsible for the purchase of the energy and pulp. "I think we can look forward to a good future and we are starting to tell the workforce about that," he says. With Chapman at the helm and development plans in place, it seems that Curtis can toast a healthy future. Curtis Factfile - 1873 Guardbridge Mill founded on site of a former whisky distillery - 1980s Firm becomes part of US-based James River Fine Papers - 2002 Management buyout brings Curtis back into Scottish ownership - 2005 Projected turnover of £32m - Staff 340 - Produces 30,000 tonnes each year of speciality grades - Certification Forest Stewardship Council (FSC) | ![]() capercaillie | |
01/12/2005 07:23 | Im not letting my stock go for a song. If it is MBO - they can graft for me rather than themselves. Can they see conditions turning the corner and trying to get it on the cheap. Large trades over last two days - I was expecting some news regarding changes in holdings. | ![]() capercaillie |
It looks like you are not logged in. Click the button below to log in and keep track of your recent history.
Support: +44 (0) 203 8794 460 | support@advfn.com
By accessing the services available at ADVFN you are agreeing to be bound by ADVFN's Terms & Conditions