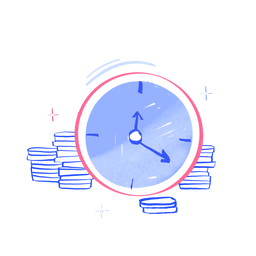
We could not find any results for:
Make sure your spelling is correct or try broadening your search.
Share Name | Share Symbol | Market | Type |
---|---|---|---|
Global Technologies Group Inc (CE) | USOTC:GTGP | OTCMarkets | Common Stock |
Price Change | % Change | Share Price | Bid Price | Offer Price | High Price | Low Price | Open Price | Shares Traded | Last Trade | |
---|---|---|---|---|---|---|---|---|---|---|
0.00 | 0.00% | 0.0001 | 0.00 | 00:00:00 |
Cement Plant Mercury Emissions Testing Using MBS
The United States Environmental Protection Agency (EPA) will implement new mercury emissions regulations in 2013 and many cement plants will not be able to meet the more stringent regulations. Some of these cement plants have installed powdered activated carbon (PAC) systems in an attempt to reduce mercury emissions to comply with the new regulations. However, mercury emissions have not been reduced enough to meet the new regulations at some of the plants.
Global Technologies Group, Inc. (Global) contracted MSE Technology Applications, Inc. (MSE) to perform a series of tests to determine if Molecular Bonding System (MBS), a metals treatment agent, can reduce mercury concentrations within a moist gas stream at elevated temperatures. MBS has historically been used to bond with metals in contaminated soils and has also been previously tested to reduce mercury emissions in a power plant with success.
Four tests were conducted using MBS, PAC and a mixture of MBS and PAC as the treatment agents to reduce mercury concentrations in a flow-through testing apparatus which simulated actual plant conditions. A picture of the test apparatus is shown in Figure 1.
The reaction column was packed with denstone, glass wool, and 10 grams of the treatment agent(s) and placed on top of the reaction flask after the system was brought to temperature. The reaction flask contained approximately milliliters 5(mL) of elemental mercury. Nitrogen flow was initiated at 0.5 Liters per minute (L/min) and allowed to flow through the water flask into the mercury flask and up the reaction column through the treatment agent(s). The water flask was heated to 130°F to produce ~ 17% moisture in the system and the mercury flask and reaction column were heated to 250°F to mimic typical cement bag house temperatures.
Test 1 used 100% PAC with a 17% moisture content. Test 2 used 100% MBS with 17% moisture content. Test 3 used 90% PAC and 10% MBS with 17% moisture content. Test 4 used 100% MBS without any moisture in the system.
The tests were all run for the same period of time, using the same gas flow rate, and the same temperatures to produce similar mercury concentrations within the mercury flask and reaction column. After the tests were completed, the reaction column was removed from the mercury flask and the treatment agent(s) were removed, mixed, split into samples and submitted to the MSE Analytical Laboratory for mercury analysis using EPA, SW-846 Method 7471. Table 1 shows the test details and mercury concentration levels for the samples submitted.
Since the cement plant currently uses PAC to reduce mercury emissions,
Test # 1 was designed to be the baseline test and used only PAC in the reaction column. The PAC removed an average of 96 mg/Kg of mercury from the vapor phase in the test system.
Test # 2 used only MBS in the reaction column and the average mercury reduction was 501 mg/Kg, indicating that MBS can remove more than five times the amount of mercury than the PAC.
Test # 3 used a combination of 90% PAC and 10% MBS and that combination of materials removed an average of 230 mg/Kg from the vapor phase of the test system. Test # 3 results indicate that the 10% addition of MBS to the PAC can remove more than twice as much mercury than the PAC.
Test # 4 was conducted to determine if MBS could reduce mercury concentrations in a dry environment, which could represent an upset condition at the cement plant. The results for Test # 4 show that MBS in a dry environment removed an average of 398 mg/Kg of mercury from the test system. The average amount of mercury that was removed from each test was plotted and that graph is presented in Figure 2.
The testing indicates that MBS removes elemental mercury vapor from a hot nitrogen gas phase. Testing is being conducted to determine if any acid gases, NOX or SOX will be generated using MBS with compressed air in the test system this week.
"The validated Mercury emissions report is part of the data that will be presented to the Portland Cement Association, EPA and other agencies of the government here in the United States and abroad. The results were impressive to both MSE and the cement plant, as the use of MBS/IFSC2 without the use of PAC can remove more than five times the amount of mercury than the PAC. I believe that now we will be the benchmark for Mercury removal and rid our people of a very dangerous airbornetoxin not only here but worldwide," stated James Fallacaro, President.
Global Technologies Group, Inc. (GLOBAL) is a company that is in the business of acquiring exclusive licenses and distribution and reseller contracts on proven technologies in the environmental, green and war fighter industries. The criteria for the licensing or distribution agreements of the technologies are: they must be proven, validated and in use. The business plan of Global is to sublicense the technologies it acquires to companies in Countries covered under the original license grants and for its own use. For our exclusive distribution and reseller agreements, we partner with appropriate representatives in the covered countries for resale of turn key projects. Solucorp Industries is the patent holder and licensor of the MBS/IFS2C technology.
Image Available: http://www2.marketwire.com/mw/frame_mw?attachid=1961130 Image Available: http://www2.marketwire.com/mw/frame_mw?attachid=1961136 Image Available: http://www2.marketwire.com/mw/frame_mw?attachid=1961139
Contact: JAMES FALLACARO Email Contact 941-685-1616 WWW.GLBTECH.COM
1 Year Global Technologies (CE) Chart |
1 Month Global Technologies (CE) Chart |
It looks like you are not logged in. Click the button below to log in and keep track of your recent history.
Support: +44 (0) 203 8794 460 | support@advfn.com
By accessing the services available at ADVFN you are agreeing to be bound by ADVFN's Terms & Conditions