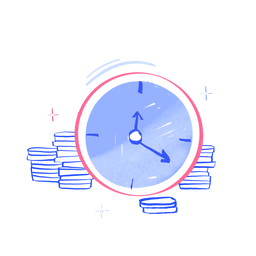
We could not find any results for:
Make sure your spelling is correct or try broadening your search.
Share Name | Share Symbol | Market | Type |
---|---|---|---|
Qell Acquisition Corporation | NASDAQ:QELL | NASDAQ | Common Stock |
Price Change | % Change | Share Price | Bid Price | Offer Price | High Price | Low Price | Open Price | Shares Traded | Last Trade | |
---|---|---|---|---|---|---|---|---|---|---|
0.00 | 0.00% | 9.41 | 9.41 | 9.55 | 0 | 01:00:00 |
Filed by Qell Acquisition Corp.
Pursuant to Rule 425 under the Securities Act of 1933
and deemed filed pursuant to Rule 14a-12
of the Securities Exchange Act of 1934
Subject Company: Lilium GmbH
Commission File No. 001-39571
Transcription – Lilium Investor Film 1
TITLECARD:
Lilium
Technology: Mission Profile and Aircraft Architecture
CAPTION Daniel Wiegand – CEO and Co-founder
0:09
We have developed a revolutionary aircraft architecture based on the combination of
CAPTION: Tech Demonstrator
ducted electric vectored thrust combined with a fixed wing aircraft configuration, and over the last six years we have refined the airplane configuration but also the underlying technologies over four different generations of aircraft which we had in flight testing.
Every airplane design starts with the propulsion system. The unique thing about our technology is that we have mastered the use of electric ducted fans and these come with a set of advantages.
The first advantage is you can put acoustic liners into the ducts similar to the engines in large airliners. And these acoustic liners capture and dissipate the noise before it propagates into the environment and this allows us to achieve market leading low noise levels.
The second advantage is that such a ducted fan is roughly 15 times smaller to lift the same weight like an open propeller system, this means the footprint of such a configuration is smaller for the same weight and we can make heavier airplanes that can carry more passengers, and this gives us the unit economics that we need for our service.
1.29
The passenger acceptance of turbo fans is much higher and this is one of the reasons that 95% of all airliners and business jets are using turbo fans in their airplanes.
After it was clear that we would use this propulsion system, we have thought about different ways of putting these engines in the aircraft configuration. We have chosen a so-called distributed electric propulsion system, and the advantage of that is we can integrate the engines into the wings, and thus eliminate the surface of the nacelle because basically the nacelle of the engine is acting at the same time as the wing.
The advantage of that is you have less weight on the airplane and at the same time you have less drag on the aircraft. The configuration is driven by the idea of simplicity. There is no aerodynamic control surfaces, there’s no water cooling systems in the engines, there’s no variable blade pitch, and the aircraft has no tail because we can stabilise with this thrust vectoring system.
1
2.32
The disadvantage of the small footprint of the ducted fan is that we consume roughly twice the power in hover flight than the standard propellor based electric VTOL aircraft. However, because we spend less than 60 seconds per mission in the hover phase and 30 to 60 minutes in cruise flight. Since we are operating an inter-city shuttle flight service this is what our mission cares about, whereas we don’t want to operate these airplanes in very extended hover times.
This configuration uniquely combines vertical take-off and landing capabilities with very high efficiency fixed wing flight while at the same time being very low noise at the take off and offering scalability to larger passenger capacity.
3.20
This is our current technology demonstrator, it’s a full scale five seat airplane and it lays out all the features and technologies which also go into our seven seat serial aircraft which we have started developing two years ago. At market entry we will already have the highest capacity in the market, 50% more than our strongest competitor and this is what we need to achieve the attractive unique economics of our service.
3.49
TITLE:
Technology
Flight Physics and Flight Control Systems
CAPTION Matthias Meiner
Phoenix Chief Engineer and Co-founder
My name is Matthias Meiner, and I am one of the four co-founders of Lilium and I met Daniel roughly four years ago when I was doing my PhD in robotics, he didn’t really need to convince me to join Lilium because I was directly so excited about the opportunity of this technology and the vision behind it.
So, I will walk you through a little bit of how the flight controls and the flight physics of this concept works.
So, we have 36 engines, and they’re distributed into 12 flaps, four of which are in the front on the canard, eight flaps on the main wing. The interesting thing about these flaps is that they’re not just used for the vertical take-off, so for the thrust generation, but they are also used throughout the whole flight envelope for all of the thrust vectoring that is needed to control every single axis of the aircraft.
4.35
And the advantage of this is, that since we need so much thrust for take-off, this gives us exceptional control authority for all of the different flight phases, and then we only have to control essentially the flap angle and the rpm of the engines and that’s all that the flight control system actually needs. So we don’t have any rudders, any other aerodynamic surfaces like ailerons and that obviously makes it much more simple and also much more efficient.
2
For vertical take-off you can imagine these flaps are all pointed downward in a vertical position and then after around 10 seconds of hover flight, where we generate the first initial altitude, they are slowly transitioning into a more horizontal position plus accelerating the aircraft and then in cruise flight all of the aerodynamic lift is purely generated by the wings and by the main body.
5.23
Since we have 12 flaps we also have a very highly redundant system. That means in case of failures that is something we have already seen in flight tests, the flight control system directly recognizes that and redistributes the thrust in a way that below a second the aircraft is stabilised again.
Caption: Test aircraft automatically stabilises after loss of three engines
This just shows that its distributed nature is not just adding a lot of control authority
but it’s also providing a lot of safety.
Another big advantage is that because we are sucking in the air over the wing since they are in the back of the wing, we are sucking in the air over the wing and that essentially creates a high-lift system so even at low speeds we are flying very efficiently, which is important because in approaches when the pilot needs that controllability and that manoeuvrability we can stay in that phase without consuming the amount of power that we would need to hover.
So over the past year’s built up extensive knowledge in flight dynamics and flight controls very specific to our concept. We have developed very extensive aerodynamic data banks and models for our engines and we combine this into a holistic flight physics model so we develop all of the core elements of our flight control system in house and that specifically means the flight control laws, the software, the algorithms behind it, and we can use our flight dynamics models to test and develop all of this code. So that we don’t have to find out if something works in flight test, but we can actually predict how the aircraft will behave way before in simulation.
And the way that we’ve done it is we’ve built a lot of simulations and we’ve combined the aerodynamic data bank created from CFD simulations with the aerodynamic deck of the engines, we’ve included power models so we can also model the power consumption in flight and we’ve combined all of this into an extensive flight dynamics model and that flight dynamics model is essentially a virtual or digital twin of the actual aircraft and we use this to develop all the flight control code.
7.23
We’ve refined this knowledge and that capability over the past generations of prototypes in such a way that actually for Phoenix we didn’t have to retune any of the flight control parameters in flight. We’ve predicted it so well that we found that actually in flight whatever we’ve flown before in simulation, worked exactly that way in real life.
That flight dynamics model is also used in our simulators, so we’ve built a VR simulator that we’re also using for pilot training, for pilot evaluations so we bring in the pilot knowledge very early on in the process, we can show it to the authorities, to EASA to FAA, and we can evaluate also code changes in the actual physics with the human in the loop so we can evaluate handling qualities, and we can make sure that the aircraft doesn’t just behave well but also controls well from a human perspective.
3
8.14
So the flight dynamics model and the software development framework together, actually mean a huge trade secret for us because we’ve built up this proprietorial knowledge over the past years very specific for our configuration.
8.27
TITLE:
Technology
Engineering
I’m Brian Phillipson and I started working in the aircraft industry 50 years ago. I spent much of my early career on the design and development of fast combat aircraft, military jets…
CAPTION:
Brian Phillipson
Deputy CTO
…including the vertical take-off and landing Harrier and the International Eurofighter Program. I then spent about ten years in design of major modifications, complex modifications, applied to Civil and military aircraft.
We have invested internally in all of the capabilities and tools that we need to develop the complex technologies that go into the aircraft, including the ducted fan engine, the battery power system, the advanced composite lightweight structure, the flight control systems, and all the complicated electronics and software required to take care of this aircraft.
We have a very wide range of computer analysis and modelling tools that allows us to investigate all aspects of the aeroplane before we start build. That includes acoustics, propulsion, thermal management, structural strength, flight controls, all aspects of the design can be assessed by computer modelling before we start ground testing.
9.32
To validate our modelling and improve our technologies, and ultimately to support certification of our airplane, we have more than 50 different test facilities and the manufacturing facilities required to support them. They allow us to assess structural performance, aerodynamic performance, thrust, propulsion, acoustic, and particularly today, we are standing in the acoustic wind tunnel which allows us to assess the acoustic performance of different fan types, different rotor types, and to measure the radiated noise as well as the propulsion efficiencies of motors.
4
A particularly important point is that we have all these analysis, design, manufacturing and test facilities co-located on our site here. That allows us to respond very quickly to new requirements, to changes and generally to accelerate the entire development and certification program.
10.19
TITLE: Technology
Batteries
One of the key enabling technologies of our aircraft are batteries. 20 years ago there were no batteries available that could have made our airplane lift off. However, thanks to the continuous improvement of energy and power densities, we are now at an inflection point that allows us to build manned vertical take off and landing aircraft.
The challenge with batteries here is that they need to fulfil often contradictory requirements. For example you need a high energy density to achieve the required range, but at the same time you need a high power density which is crucial for take-off and landing of the aircraft.
We’ve not only looked at battery cells, we’ve also looked at the surrounding technologies. For example, we have developed a lightweight module casing which can contain the fire of an entire module, and allows the aircraft to do a continued safe flight and landing in those worst case conditions.
From an economic point of view, we want batteries that can be manufactured in existing manufacturing lines and are low cost, and at the same time have a high cycle life and fast charge capability.
11.34
TITLE :
Technology
Ducted, Electric
Fan Engines
Caption: Alastair McIntosh
Chief Technology Officer
I’m Alastair McIntosh. I’ve been with the aviation industry for more than 30 years, mainly working with Rolls Royce, where I worked in jet engines. I was accountable for the delivery of the Trent XWB, for the A350, and also the BR725 for the Gulfstream flagship aircraft, the G650.
Strategic choices have been taken to go with electric ducted fans, as opposed to open rotors. They offer a number of advantages in comparison to an open propellor. What you actually see then is a significant number of blades in the rotor itself in the fan. Now the reason we do that is to optimise mainly for noise and also for aerodynamic efficiency and performance.
5
The rotors themselves is one part, but also the structure at the back what we refer to as the stators, that’s the other area. Matching the two of those aerodynamically is not only good for efficiency but very, very good for noise. The duct actually contains the noise, that means that the noise can only be projected either forward or rearward. So that’s one of the great advantages that’s offered by this technology when comparing it to an open rotor.
12.50
Within the duct itself, we can then apply what we refer to as acoustic liners. Those liners will actually absorb more of the noise energy that’s present into the system and, quite literally, dampen those down or tune them out. And we’re targeting to keep that noise as low as possible. The ducted fan is a very efficient system to lifting aircraft. The fan has to work quite hard in comparison to an open propellor for a given diameter, but has the advantage that it’s a very efficient system because it has a reduced over-tip leakage. What that means actually is that see a benefit of roughly about 40% in efficiency.
It also gives us some other benefits: we can match very well the engine in a manner that where we take a lot of flow through the ducted fan for take-off, actually we don’t need so much flow when we are in cruise. We actually only need about 10% of the thrust roughly in comparison.
What that actually means then, is that we need to match the fan performance at cruise. And the way we do that is we change the geometrical area at the back of the engine. So, what we have there then is a variable nozzle.
We control the variable nozzle by a very simple mechanism, as the angle of the ducted fan changes there is a mechanical link which then closes down that area hence it gets us the best performance that we require, both in hover and in cruise. We actually only spend a very small amount of time in hover either in take off or in landing. That is one of the misconceptions that isn’t fully understood, I think, when people stare at the Lilium jet and wonder whether it is a viable concept or not.
14:39 minutes
6
1 Year Qell Acquisition Chart |
1 Month Qell Acquisition Chart |
It looks like you are not logged in. Click the button below to log in and keep track of your recent history.
Support: +44 (0) 203 8794 460 | support@advfn.com
By accessing the services available at ADVFN you are agreeing to be bound by ADVFN's Terms & Conditions